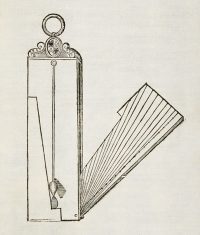
This drawing, found in the Galileo Museum in Florence, shows an instrument used to measure the slope or elevation of an object over a broad area with respect to gravity. It is an inclinometer, a rather simple yet effective tool that has been used for centuries.
The development of electronic and MEMS-based (micro-electro-mechanical systems) inclinometers arrived much later with modern technology, revolutionizing various fields such as aerospace, civil engineering, and railway transportation.
The land angle information inclinometers provide can help determine stability, potential shifts, and structural integrity in many applications. According to the context and purpose of use, inclinometers can be strategically installed inside boreholes, retaining walls, bridges, rail tracks or track stabilizers, heavy machinery, aircraft, and many other places. The data can be monitored and collected from sources such as portable readout devices, data loggers for real-time data transmission, or MEMS-based sensors connected to SCADA systems or cloud platforms for remote monitoring. Thanks to the integrated and improved technologies, the modern inclinometers ensure safety and stability with a more versatile approach.
Jewell Instruments specializes in designing and manufacturing high-precision products. Their expertise spans inclinometers, electronic compasses, avionics compasses and components, solenoids, panel meters, and acceleration and tilt sensors.
Jewell Instruments has two main categories of inclinometer products; Force-Balance inclinometers and MEMS inclinometers.
Force-Balance Inclinometer’s Structure and Measurement Method
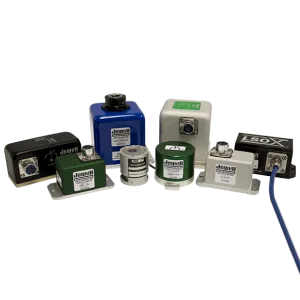
Force-balance method inclinometers are electromechanical sensors used in measurements that require high precision:
- Fundamental Structure
Includes a pendulum or moving mass within the sensor.
The mass is sensitive to tilt due to gravitational forces, creating an angular deviation.
Mass movement is usually measured with a capacitive, inductive, or optical detection mechanism.
- Feedback Mechanism
An electromagnetic feedback coil is activated after detecting mass movement.
This coil applies force-balance feedback force to keep the mass in its original, neutral position.
The balancing force applied is directly proportional to the tilt angle and is used as the system’s measurement output.
- Benefits
High Precision: Measures down to the microradian (µrad) level.
Wide Range: Covers angles from ±0.01° to ±90°.
Shock & Vibration Resistant: Feedback system minimizes external impact.
Low Hysteresis: Ideal for high-accuracy applications.
Force-balance technology is especially used in applications where low-frequency movements need to be measured accurately. Aerostructure testing is one of those applications. With an increasing need for lightweight designs without compromising quality and affordability, extensive testing became crucial in product development and implementation. Aerospace is one of those applications that cannot afford risks so it is governed by strict standards and required accreditation.
Aerospace testing involves tensile, compressive, flexural, and fatigue tests to ensure structural integrity and durability. Various sensors are used to meet strict testing standards. Testing conditions simulate real-world stressors such as temperature extremes, humidity, altitude, vibration, shock, and acceleration.
Jewell Instruments’ inclinometers have proven to be a suitable sensor solution for aerostructure testing. During testing, precise angular displacement control is crucial. Jewell Instruments’ LCF-300 inclinometer offers:
- 1 microradian resolution for high-precision feedback.
- Fluid damping to filter out noise, vibrations, and crosstalk.
- ±1° to ±90° range, designed to withstand high shock and vibration environments.
- Low hysteresis & excellent repeatability, ensuring reliable performance.
With its advanced features, the LCF-300 inclinometer plays a vital role in accurate aerospace testing and in-service life predictions.
MEMS Sensors for Industrial Applications
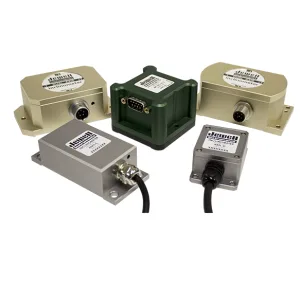
While MEMS sensors have been around for many years, they gained recognition in industrial control applications rather recently. The early MEMS had unfixed problems with drift, noise, repeatability, etc. Now with enhancements based on modern demands, MEMS technology provides budget-friendly yet high-precision solutions.
- Jewell Instruments’ MEMS inclinometers offer a temperature range of -40ºC to +85ºC which makes them useful for manufacturing automation applications where extreme temperatures are a factor.
- Although not as rugged as force-balance sensors, MEMS inclinometers have a vibration resistance of 10grms at 10-1000Hz. This value is more than enough for industrial measurement and control, drilling equipment, platform leveling, and even geotechnical monitoring.
- Most Jewell Instruments’ inclinometers come with an IP67 rating. This guarantees that their housing is protective enough to be submersed in shallow water temporarily, making them suitable for offshore monitoring or subsea pitch and roll applications.
Throughout decades of hard work and excellent engineering, Jewell Instruments gained massive success and continued customer satisfaction. Jewell Instruments’ experience and knowledge in sensing solutions ensures versatility across all industries.
Interested in more? Find more Jewell Instruments products here: